Another country, another record
by Chandrika Sen
Mumbai: Afcons Infrastructure Ltd (Afcons) ventured into Guinea with the bauxite handling facility project for Guinea Alumina Corporation (GAC). This country, on the west coast of Africa, is the largest producer of bauxite ore in the world, and, its economy largely depends on bauxite export. In the light of this, the project gains significance as it has a direct impact on the country’s economy.
“In our maiden project in Guinea, we have set a record of carrying out one of the heaviest lifts in Afcons’ history while putting together the railway car dumper and stacker reclaimer. This under-construction bauxite export facility is probably the largest in Guinea, and, Afcons is proud to be a part of it,” says Mr Rajendra Deshmukh, GM, Contracts and Project Controller for the Guinea project.
Afcons was entrusted with the civil and mechanical works of the port handling system by Shapoorji Pallonji EPC, the main contractor; Guinea Alumina Corporation (GAC) being the main client. The bauxite handling facility is spread over 5 kms of the port area. “While the job seemed routine at the start and we had strategies in place, there were some delays that set us back in terms of time. That’s when the team adopted innovative approaches. Two 750 MT capacity cranes were mobilised from Europe to complete the critical activities of assembly and erection of the railway car dumper and stacker reclaimer,” he says.
The RCC work for building the car dumper started from 25m below ground level. According to the initial plan, the structure was to be in-situ assembled with pieces of 30-35 MT being lowered 13m below ground level. However, this plan had to be dropped in order to make up for the lost time. “While the civil works were going on, another team assembled the mammoth 450MT structure on the site. The car dumper was then shifted to the spot via a Self-Propelled Modular Transporter (SPMT) and lowered into the car dumper unit with the help of the two 750 MT capacity cranes,” says Deshmukh.
The 1600 MT stacker reclaimer was initially supposed to be assembled in pieces of 35-40 MT, and one 400 MT crane was supposed to be used to put this structure together. “However, due to change in scenario, we assembled various units, including single unit of 250MT. The cranes were brought in to assemble the entire structure. We were again able to save time on this activity owing to innovation,” adds Deshmukh.
“I am proud of my team. The way we worked in the face of challenges is a testimony of our efficient project management skills. By adopting these strategies, we were able to offset delays and a substantial work has been completed within the original schedule,” says Deshmukh.

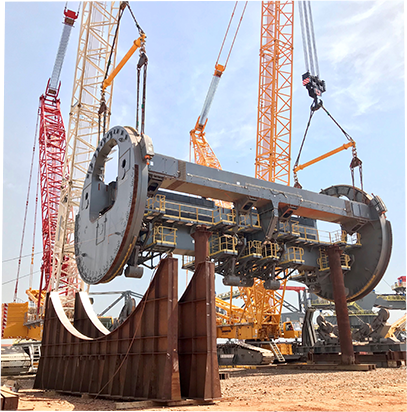

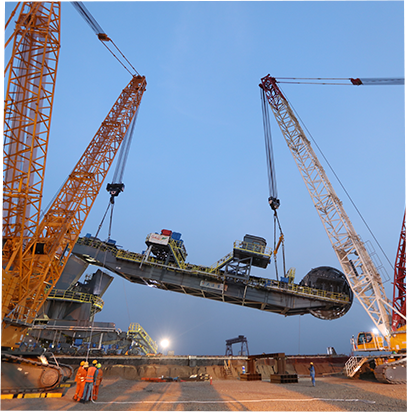