The HIGH spot!
The Katra-Dharam section of Udhampur-Srinagar-Baramulla Rail Link Project in Jammu & Kashmir is one of the most challenging infrastructure projects in India. Not just the geography and geology, but the engineering execution must be of highest order in this region. Afcons is constructing 16 bridges in this section at four different locations. The sheer operation complemented by innovations and grit is an X-factor.
While the team has been conquering this terrain one pier at a time, there was one challenge which needed a perfect combination of planning, resource allocation, innovation, and, implementation to be overcome. For bridge 87, the team had to protect a vertical cut of approximately 65m by shotcreting. While the location of this project involves many such vertical cuts, this was way more challenging than initially forecast.
Firstly, the team faced a highly decomposed surface on an extremely steep location. Shotcreting was not possible using any machine, and hence, the Aliva shotcrete machine, with a capacity of 9 cum/hr, was specifically chosen for the task. Choosing the right machine proved to be a crucial step as this machine is easily portable, light in weight, which were the important factors. But that also meant negotiating some technical hiccups.
The machine’s standard spraying capacity if only up to 15m vertically and 35m horizontally. To increase the reach, the team modified the length of the hose pipe to up to 65m. This modification made it easier to cover the entire surface. Also, the team used high capacity 650 CFM compressor to increase the bar pressure for spraying up to 7 from the usual range of 4-5. The spraying was done using a 30MT crane and man-basket that carried nozzle to required heights and widths. This reduced the risk of dealing with decomposed strata.
Environmental challenges extended beyond the strata. The dipping temperatures, up to freezing point in winters, and, consistent strong winds were major obstacles. The team decided to change mix design for easing the pumping of high slump shotcrete. The usual 150-160mm shotcrete slump was replaced by 190-210mm shotcrete that further helped in the process.
The accelerator (chemical) was also increased in order to help the shotcrete set instantly, and, help reduce wastage - a dual advantage. The requirement of shotcrete layer was of 100mm, but the team did it in two rounds. First, a layer of 50mm was sprayed and allowed to set, and then the second layer of 50mm was sprayed across the surface, making it perfect.
It was the unification of all these things that resulted in successful completion of the task. Easier said than done, surely. It took 433 cum of shotcrete and a 15-day marathon work for the team to achieve what it set to do. The mountain had been conquered, in all senses. Kudos to Mr D P Singh and his project team, the heroes that have been giving it all for this project to be ready as quickly, and as swiftly as possible.

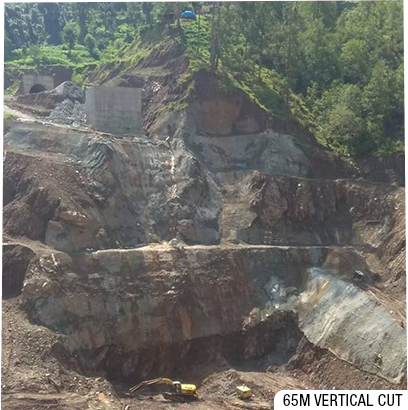

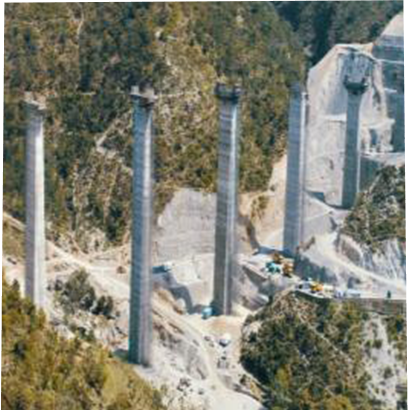