Environment over everything
The Mahatma Gandhi Setu is one of India’s longest river bridges, stretching 5.575km over river Ganga. It connects Hajipur in North to Patna in South Bihar, and, is considered as the lifeline of the state. Today, it is estimated that over one lakh vehicles, and, over 20,000 pedestrians ply on this bridge daily. The original bridge was not designed to accommodate this volume, and, with continuous wear & tear, repairs, and, rehabilitation works, it was imperative that the superstructure of the bridge was replaced.
Afcons was assigned this task and the project team began the rehabilitation work facing a very big challenge right at the face of it. During the entire project, the traffic could not be completely stopped. So, the strategy was set, and, the work was divided in two phases. In the first phase, the traffic from upstream lane is diverted onto the downstream lane, for dismantling and rehabilitation of upstream lane. Later in second phase, the downstream lane will be closed traffic will be diverted onto the new upstream lane, and the work on downstream lane will begin. The dismantling is also divided in two parts, for spans over land & seasonally dry land, and, spans over water. So how did the team carry out the entire operation without affecting the environment?
Dismantling over land/seasonally dry land
The dismantling of piers P1 - P26 is over land. This is done using high reach boom jaw crusher, after careful de-stressing of externally prestressed cables in a phased manner from both the ends. Notably, the High Reach Boom Jaw Cutter has been designed and assembled in house that crushes concrete and cuts through steel cables and rebar. During the entire process, keeping an eye on environment, gigantic tarpaulin is laid on land before crushing to prevent contamination of top soil. Additionally, anti-dust suppression systems are also deployed to keep in check the dust pollution in the surrounding areas.
The span segments above seasonally dry spans from Pier P27 - P36 are cut with the help of high capacity wire saw cutters and lowered by cantilever gantry anchored over the spans on each end. The dismantling is done simultaneously from each end of the span arms in synchronisation. The gigantic tarpaulin is used on the riverbed to prevent rubble from falling on it.
Dismantling over river
For the piers in water span, P37 - P46, the operation becomes even more delicate. As this is an environmentally sensitive area, and the work is carried out over the Holy River Ganga, extra precautions were in place. These spans are dismantled in such a way that not a single debris falls in the River. First, the stress cables are exposed carefully with a pneumatic drill. They are cut off using a flame cutter. After the dismantling of segments, the pierhead in water spans are cut with wire saw cutters and lowered by cranes in pieces, leaving only 0.7m above the bottom slab for manual chipping and exposing rebars. The lowered pieces over barges are then unloaded at a temporary jetty and sent to debris handling yard. For manual chipping process, heavy duty safety nets are installed to capture chipped debris, and the waste is disposed safely ensuring not a single debris falls into the river during this process too.
Recycle and reuse
Once the dismantling is done, the collected debris from land and water spans is transported to the handling yard where it is crushed using resizing buckets up to 40mm. The reinforcement steel is separated for stacking and disposal. The steel and concrete waste is stacked separately for reuse and disposal. The resized aggregate waste is re-utilised in temporary works and approach roads’ development facilitating easy movement of equipment at the site. The balance waste is being disposed of in a pre-planned environment-friendly way, making sure that no element is treated without keeping the environment in mind.
After the dismantling of superstructure, the construction of the new superstructure begins. A new steel truss structure weighing 720 tonnes each is erected between the modified pier caps. While the erection of trusses on land is carried out using a Ground Support System, for the spans in water region, cantilever erection methodology is used. Slowly and steadily, the first lane of the bridge is nearing completion.
The rehabilitation of this behemoth is certainly complex and challenging. Especially, the dismantling process, keeping in mind the environment aspect was a huge challenge. It is being done in a very organised and systematic fashion, despite the challenges of ongoing heavy traffic, river swelling in rainy seasons etc. while being sensitive to the environment in and around the Holy Ganga. The project involves dismantling of concrete to the tune of about 75000 cum, which arguably, has never been attempted in India earlier. And to do that by being completely environment-friendly is no mean feat! Kudos to the MG Setu team!

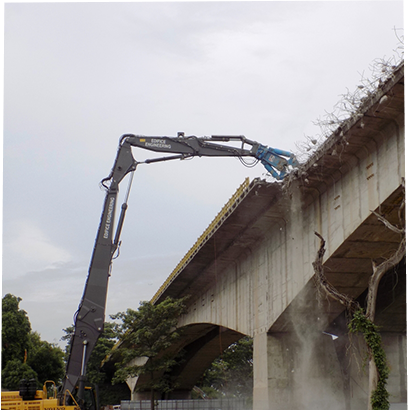

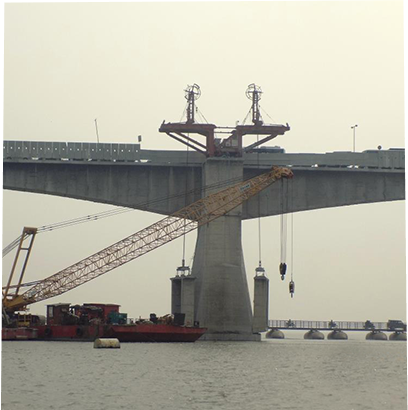